6 Essential Questions Contractors Should Ask Their Fire Door Manufacturer – Insights from YK Fire Door
At YK Fire Door, one of the leading China fire door manufacturers, we are often approached by contractors, developers, and real estate professionals with practical yet critical questions before finalizing their fire-rated door procurement. Their concerns are valid—selecting the right fire door manufacturer is not a checkbox task. In today’s safety-driven construction landscape—whether in hospitals, schools, high-rises, or industrial sites—products like fire rated wood doors, steel commercial doors, and wooden fire resistant doors must meet rigorous performance and compliance standards. These are not off-the-shelf solutions; they demand certified materials, precision production, and a commitment to lifecycle support.
This article addresses six of the most frequently asked questions from our global clients. Our goal is to help contractors and building professionals make informed, compliance-focused decisions when choosing a fire rated door company or commercial door manufacturer—decisions that ultimately protect lives and reputations.
1. Are Your Fire Doors Certified to International Standards (e.g., UL, CE, BS, EN)?
The First Question Every Responsible Buyer Must Ask: “Are Your Fire Doors Fully Certified to International Standards such as UL, CE, BS, or EN?“
At YK Fire Door Manufacturer, we emphasize this question above all others. As a leading China fire door manufacturer and long-standing fire rated door company, we know that the difference between a certified fire door and a non-certified one is not just technical—it’s existential. When selecting a fire door supplier, certification isn’t a checkbox; it’s your front line of defense against legal liability, asset loss, and, most importantly, threats to human life.
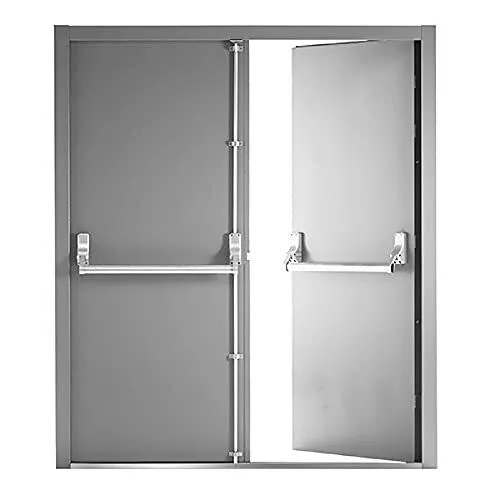
Why Certification is Not Optional—It’s Foundational
A fire rated door is a highly engineered safety system. Whether you’re installing fire rated wood doors in residential spaces or steel commercial doors in industrial facilities, the integrity of the door assembly—door leaf, frame, intumescent seals, hinges, and closers—must be verified through rigorous third-party testing under international standards such as UL 10C, EN 1634-1, or BS 476-22.
Certified wooden fire resistant doors, for instance, are designed to maintain compartmentation, delay the spread of fire and smoke, and protect vital evacuation routes. They aren’t simply decorative panels—they’re tested barriers built to withstand high temperatures and pressure for durations of 30, 60, 90, or even 120 minutes. At YK, we regularly manufacture and supply 90 minute fire rated wood doors and fire exit doors that meet or exceed global benchmarks.
Legal, Financial, and Ethical Consequences
Uncertified doors don’t just fail in emergencies—they expose you to extensive liabilities. Building regulations for fire doors worldwide, including those under NFPA, IFC, and Eurocode, require compliance with standards like UL 10C and EN 1634-1. Procuring from a fire door supplier without proof of compliance can invalidate insurance policies and breach regulatory frameworks.
YK’s products—ranging from fire door garage models to wooden fire doors for high-rise residences—are backed by full documentation, third-party testing, and ongoing factory audits. We also help international partners understand region-specific compliance needs, especially when working with our clients as a China fire door supplier for the European, Middle Eastern, and North American markets.
Understanding the Standards: Not All Certifications Are Equal
Our international team works daily with building owners, architects, and contractors to help them decode the complex world of fire door certification:
- UL 10C: North America’s go-to standard for positive pressure testing.
- UL 9: Required for fire-rated glass and vision panels.
- EN 1634-1: The EU’s leading fire resistance standard, used widely for CE-marked doors.
- BS 476-22: Still recognized in the UK, especially in legacy infrastructure.
Whether it’s a fire rated steel door for a commercial warehouse or a fire door closer compliant with door closer fire regulations, YK ensures that every component matches the standard down to the smallest detail.
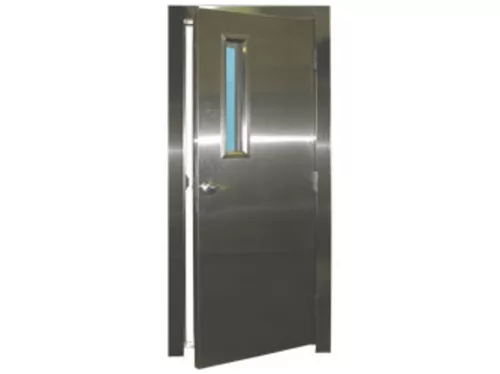
Real Certification—Not Marketing Spin
True fire certification covers more than a label. It verifies the entire door assembly, including frame profiles, glazing units, seals, locksets, and closers. A genuine commercial door manufacturer provides:
- Assembly-specific certification reports.
- Declaration of Performance (DoP) for CE-marked models.
- Factory Production Control (FPC) audit results.
- Permanently affixed traceable labels (e.g., UL mark, EI60 stamp, FD60 tag).
YK guarantees full traceability for every fire rated wood door and steel fire door we export. We reject substitutions and enforce a strict “no deviation” policy for materials and hardware.
Trust but Verify—Your Procurement Checklist
Before selecting any fire door manufacturer, especially for commercial or multi-occupancy applications, ask the following:
- Are the doors tested as a complete assembly?
- Can you provide documentation from UL, CE Notified Bodies, or UKAS?
- Do the doors include permanent certification labels with serial numbers?
- Is the supplier audited regularly for production consistency?
At YK, we’re proud to say “yes” to all of the above. Our role as a global fire door supplier—especially as a China fire door manufacturer—means we must meet and exceed not only international certification thresholds but also the scrutiny of multinational contractors, inspectors, and code authorities.
2. Can You Provide Valid Fire Test Reports and Classification Certificates?
The Paper Trail That Saves Lives: Why Valid Fire Test Reports & Classification Certificates Are Non-Negotiable
In the high-stakes procurement of fire doors, glossy brochures and smooth sales talk are meaningless static. The true measure of a door’s life-saving potential lies not in promises, but in cold, hard, verifiable documentation. Asking a supplier, “Can you provide valid fire test reports and classification certificates?” isn’t a formality; it’s a forensic demand for proof of performance. Failure to secure and scrutinize these documents isn’t just negligence; it’s gambling with lives, assets, and legal liability. Here’s why these papers are your ultimate shield and how to dissect them like a seasoned auditor.
Beyond the Certificate: Understanding the Documentation Hierarchy
Suppliers often present a single “certificate” as the golden ticket. Savvy buyers know this is insufficient. Genuine compliance requires a suite of interlinked documents, each playing a critical role:
- Classification Certificate / Certification Report: This is the top-level document issued by the accredited third-party body (UL, LPCB, notified body for CE, etc.). It states:
- The manufacturer and specific product range covered.
- The exact fire resistance rating achieved (e.g., UL 90 min, EI60, FD60S).
- The specific international standard(s) met (e.g., UL 10C, EN 1634-1, BS 476-22).
- The unique certificate number and validity period.
- Crucially: The Scope of Certification – detailing the precisely tested assembly configurations (door leaf type, core, dimensions, frame profile, hardware types/positions, seals, glazing details, installation methods). This scope is sacrosanct; deviate from it, and the certificate is void.
- Fire Test Report(s): This is the raw, unfiltered evidence. Issued by the accredited test laboratory after physically subjecting a representative door assembly to the furnace. It details:
- The Exact Test Standard & Procedure: Precisely how the test was conducted.
- The Specific Assembly Tested: A meticulous bill of materials – down to hinge manufacturer, model number, and placement; intumescent seal type and location; lock model; glazing bead profile. This is the blueprint you MUST match.
- Instrumentation Data: Temperature readings on the unexposed face (critical for Insulation ‘I’ ratings), furnace pressure, deflection measurements.
- Chronological Log: A minute-by-minute account of the test, noting when flames first penetrated (integrity failure), when temperature limits were exceeded (insulation failure), structural collapse, or any other anomalies.
- Photographic Evidence: Visual proof before, during (showing flame patterns, seal activation), and after the test. Reveals how the assembly performed and failed.
- Conclusion: Did the assembly meet the target rating under the specific standard? Why or why not?
- Tested Specification Sheet: Derived from the test report, this is the manufacturer’s formal document outlining the exact configuration that passed the test. It is the buyer’s purchase bible. Any deviation requires re-certification.
- Declaration of Performance (DoP) – CE Marking Essential: For CE-marked doors, this is the legally binding document where the manufacturer declares the fire performance classification (e.g., EI60) based on the test evidence and conformity assessment. It must reference the test report and notified body (if applicable).
- Factory Production Control (FPC) Audit Reports: Proof that the manufacturer’s quality system is audited regularly by the certification body. This ensures ongoing production consistently matches the tested and certified assembly. A certificate without current FPC audits is a historical relic, not a guarantee of current quality.
Why “Valid” is the Operative Word: Exposing the Documentation Minefield
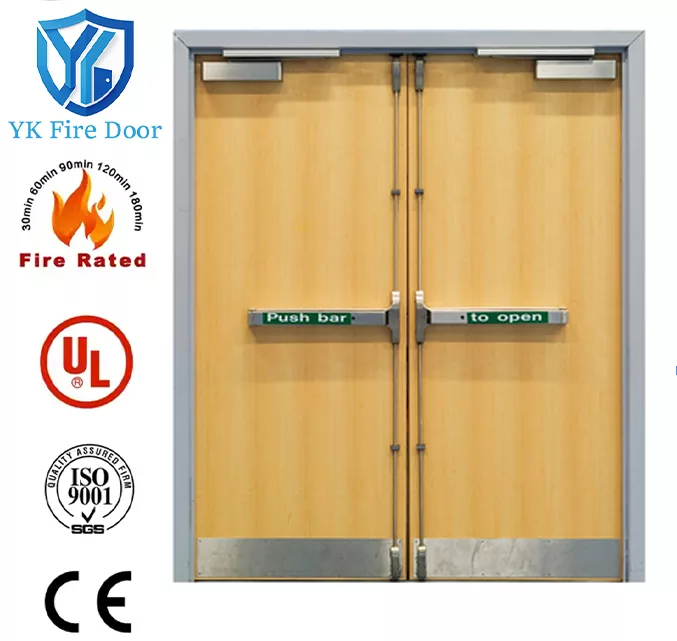
A supplier saying “Yes, we have certificates” is the starting whistle, not the finish line. “Valid” means:
- Current & Active: Certificates have validity periods (often 1-5 years) requiring renewal audits. Expired certificates are worthless. Check issue and expiry dates meticulously.
- Relevant to YOUR Assembly: Does the scope cover the exact door type, size, hardware, glazing, and frame you are buying? A certificate for a solid-core door is irrelevant to a glazed door. A certificate listing “Hinge: ABC Model 123” is void if you install “XYZ Model 456”.
- Issued by an Accredited Third-Party: Self-issued “certificates,” certificates from obscure or non-accredited bodies, or “in-house test reports” are red flags. Verify the accreditation of the certification body (e.g., UL, LPCB (UK), notified body number for CE, UKAS accreditation).
- Based on Full-Scale Testing: Beware of certificates based solely on “extrapolation,” “similarity,” or “component testing.” Fire doors must be tested as complete assemblies. A hinge tested alone doesn’t predict the door’s performance.
- Complete & Unaltered: Demand the full test report, not just a summary or cherry-picked pages. Look for original lab headers, signatures, and stamps. Digitally altered reports are a known fraud risk.
- Traceable: The certificate number and test report number should be traceable back to the issuing body’s database (e.g., UL Product iQ, BWF Certifire database, notified body listings).
The Forensic Buyer’s Checklist: Verifying Validity & Relevance
Don’t just collect documents; dissect them. Here’s your investigation protocol:
- Demand Upfront: Make submission of all relevant documents (Certificate, Full Test Report, Tested Spec Sheet, DoP, FPC Audit Summary) a mandatory requirement in the RFQ. Reject bids that omit them.
- Verify the Issuer: Confirm the certification body’s accreditation:
- UL: Check UL Online Certifications Directory.
- CE/EN: Verify the notified body number on the EU NANDO database. Check the DoP references the correct body.
- UKCA/BS: Verify UKAS accreditation of the certifier (e.g., LPCB, BSI, Exova BM TRADA).
- Scrutinize Dates: Is the certificate current? Is the test report the latest one underpinning the current certificate? Are FPC audits up-to-date?
- Match the Scope to Your Spec: Line-by-line comparison:
- Door Leaf: Core material, thickness, facing material? Exact match?
- Frame: Material (steel, timber), profile, wall fixing method? Identical?
- Hardware: HINGES: Manufacturer, model, quantity, size, placement (distances from top/bottom)? LOCKS/LATCHES: Exact model? CLOSERS: Model and grade? SEALS: Intumescent and smoke seal type, location (frame, door, or both)? GLAZING: Type of glass, bead system, maximum size/area per leaf? Any deviation invalidates the rating.
- Dissect the Test Report:
- Check the Lab: Was the test performed by an ILAC-accredited laboratory?
- Review Performance Data: Did the assembly pass comfortably or scrape through? Look at time-to-failure margins and temperature rise data.
- Examine Anomalies: Did the report note any issues during the test (e.g., excessive deflection, early flame flicker) even if it ultimately passed? This indicates potential fragility.
- Check Photos: Do they show the actual tested assembly matching the spec sheet? Look for seal activation patterns and failure points.
- Cross-Check Online: Use the certification body’s database to verify the certificate number, scope, and status using the unique identifier. Does it match the paper document?
- Beware Obfuscation Tactics:
- “The certificate covers a range”: Demand proof your specific configuration is explicitly listed within that range on the tested spec sheet.
- “Our hardware is equivalent”: Reject this. Certification is assembly-specific. “Equivalent” is unproven and dangerous.
- “The report is confidential”: Demand a full report under NDA if necessary. Summaries are insufficient. Reputable labs provide full reports to the manufacturer for client review.
- “We test annually”: Annual testing of the same assembly is unusual. FPC audits ensure consistency; re-testing usually only happens if the design changes significantly. Clarify what “annual testing” actually means.
The Consequences of Paper Failure: When Documentation Lies or Lacks
Procuring doors without valid, relevant, and rigorously verified documentation isn’t just a paperwork error; it’s catastrophic risk:
- Voided Certification & Performance Failure: An uncertified assembly is an untested assembly. It may fail catastrophically in minutes during a real fire, breaching compartmentation.
- Legal & Regulatory Breach: Installing non-compliant fire doors violates building codes and fire safety regulations (e.g., Regulatory Reform (Fire Safety) Order 2005 (UK), NFPA 80/101 (US), local fire codes globally). This exposes building owners, facility managers, contractors, and even specifying engineers to criminal prosecution and unlimited liability in the event of fire-related injury or death.
- Invalidated Insurance: Insurers rely on compliance. Non-compliant fire protection is a common ground for denying claims after a fire, potentially bankrupting a business.
- Reputational Ruin: News headlines exposing the use of uncertified or fraudulently certified fire doors following a fatal fire are devastating and permanent.
- Moral Failure: Knowing the risk existed due to inadequate due diligence is an unbearable burden.
Beyond Procurement: The Lifelong Chain of Evidence
Valid documentation isn’t just for buying; it’s the foundation for the door’s entire lifecycle:
- Installation: The certified specification is the installation manual. Installers must follow it exactly (hinge placement, seal application, frame fixing). Document installation compliance with photos and checklists.
- Inspections: Competent fire door inspectors require the original test report and spec sheet to know what to check. How can they verify hinge type or seal location without the blueprint? Provide inspectors with this critical documentation.
- Maintenance & Repairs: Replacing hardware? Only the exact certified components can be used. Any modification requires consultation with the manufacturer and potentially re-certification. The spec sheet is the repair bible.
- Asset Management & Due Diligence: During building sales, refurbishments, or fire investigations, proof of compliant fire doors via valid, traceable documentation is essential evidence.
3. What Fire Ratings Are Available for Your Doors (e.g., 30min, 60min, 90min, 120min)?
The Critical Nuance Every Buyer Must Master: “What Fire Ratings Are Truly Available for Your Doors (and What Does That Actually Mean for My Building)?”
Selecting a fire door isn’t about picking a number – 30, 60, 90, or 120 minutes – off a menu. It’s a precision engineering decision dictated by the building’s design, occupancy, escape strategy, and legal requirements. Asking a supplier, “What fire ratings are available?” is merely the opening gambit. The real questions delve into the meaning behind those numbers, the scope of the certification, and the specificity required for your project. Misunderstanding or misapplying fire ratings isn’t just a technical error; it’s a potentially lethal gamble with compartmentation integrity. Here’s how to navigate this critical terrain.
Beyond the Minutes: Demystifying Fire Resistance Ratings
A fire resistance rating (e.g., FD30, EI 60, UL 90 min) signifies the minimum duration, under standardized test conditions (like UL 10C, EN 1634-1, BS 476-22), during which a complete door assembly maintains its ability to perform three critical functions:
- Integrity (E): Preventing the passage of flames and hot gases through the assembly. Failure is visible flame penetration or sustained flaming on the unexposed side.
- Insulation (I): Limiting the temperature rise on the unexposed face (typically measured at specific points) to prevent ignition of adjacent materials or injury to escaping occupants. Common limits are 140°C average or 180°C at any single point above ambient.
- Load-bearing Capacity (S – Rarely for Doors): Primarily for structural elements like walls. Fire doors are generally non-loadbearing, so this is less common.
Key Rating Classifications:
- FDXX (BS 476-22): Fire Door rating (e.g., FD30 = 30 minutes integrity). Historically common in the UK. Does not inherently include insulation criteria. FD30S (S = Smoke) adds cold smoke leakage control.
- EXX / EIXX (EN 1634-1 / CE Marking):
- EXX: Integrity only rating (e.g., E30 = 30 mins integrity).
- EIXX: Integrity AND Insulation rating (e.g., EI60 = 60 mins integrity AND insulation). This is the most common and crucial requirement for compartmentation doors. EI ratings can also include EWXX (Radiation Control) for specific high-risk scenarios.
- UL XX Min (UL 10C / UL 10B): Indicates the duration (e.g., UL 90 min) achieved under the UL pressure test. UL listings inherently require the assembly to prevent the passage of flame and hot gases sufficient to ignite cotton waste (integrity) and limit temperature rise on the unexposed side (insulation) for the rated time. Look for the specific category (e.g., “3 Hour” for 180 mins).
Why “Available” is Only Half the Question: The Critical Nuances
A supplier listing “30, 60, 90, 120 min” ratings tells you almost nothing useful. The devil is in the profound details:
- Integrity (E) vs. Integrity AND Insulation (EI): This is paramount. A door rated only for Integrity (E60) might hold back flames for 60 minutes, but the unexposed side could become hot enough to ignite combustibles or severely burn evacuees long before that. For almost all compartmentation doors separating escape routes or occupied areas, an EI rating is mandatory. Never assume an “FD60” or “60 min UL” door automatically provides insulation unless explicitly stated as EI60 or confirmed in the UL listing details. Ask explicitly: “Does this XX minute rating include both Integrity (E) AND Insulation (I)?”
- Assembly-Specific Rating:A rating applies ONLY to the EXACT assembly tested and certified. This includes:
- Specific Door Leaf: Core material, thickness, facings, construction method.
- Specific Frame: Material (steel, timber), profile, fixing method.
- Specific Hardware: Precise hinges (model, size, number, placement), locks/latches, closers, coordinators.
- Specific Seals: Intumescent seal type, location (frame groove, door edge, both), and smoke seal type/location.
- Specific Glazing: Type of fire-resistant glass, glazing bead system, maximum vision panel size/area per leaf.
- Ask: “Show me the tested specification sheet proving this XX minute EI (or UL) rating for the exact door type, size, hardware set, and frame profile I am specifying?”
- Ratings for Different Configurations: A manufacturer might offer a solid core door achieving EI 120, but the same door leaf with a large vision panel might only achieve EI 60. A steel door might achieve a higher rating than a timber door of the same nominal thickness. Ratings are not transferable between configurations. Ask: “What is the maximum vision panel size/area permitted to maintain the EI XX rating for this specific door leaf? Does the rating change with different hardware (e.g., using a mortise lock vs. a cylindrical lockset)?”
- The “Available” Myth: Suppliers may claim a rating is “available,” implying they can make a door to that standard. However, unless they can provide current, valid third-party certification (referencing UL, EN, BS) specifically for the configuration you need, that claim is meaningless. “Available” must mean “certified and documented now for this assembly.” Ask: “Can you provide the valid UL listing, Classification Certificate, or DoP proving the EI XX rating for this exact assembly, right now?”
- Matching the Building’s Fire Strategy: The required rating is dictated by:
- Building Codes & Regulations: NFPA 101 (Life Safety Code), International Building Code (IBC), European national building codes implementing Eurocodes, UK Building Regulations Approved Document B. These specify minimum ratings based on occupancy type, building height/area, compartment size, and proximity to fire service access.
- Fire Compartmentation Drawings: Developed by fire engineers, these define the required fire resistance periods (FRP) for each compartment wall/floor and the doors within them. A door in a 60-minute compartment wall typically needs at least a 60-minute EI rating. A door protecting a stairwell serving as a “protected escape route” in a high-rise may need 90 or 120 minutes.
- Escape Time Analysis: The rating must provide sufficient time for occupants to escape the compartment or reach a protected refuge before the door fails.
- *Ask: “Based on my building’s occupancy type [specify], height [specify], and the location of this door [e.g., corridor, stairwell, compartment wall], what is the minimum legally required EI rating? Does my fire strategy require a higher rating?” (Consult your fire engineer/architect).
The Procurement Minefield: Rating Pitfalls & Deceptive Practices
Buyers face significant risks when navigating ratings:
- The “Integrity Only” Trap: Suppliers may quote a cheaper door with only an E rating (or an old FD rating without insulation proof), knowing buyers often assume insulation is included. This is catastrophic for life safety.
- “Up to XX Minutes” Claims: Vague claims like “rated up to 90 minutes” are meaningless. Demand proof for the specific rating you need on the specific assembly.
- Component vs. Assembly Rating: A supplier might claim “the core is rated for 120 minutes.” This is irrelevant. Only the complete assembly’s test result matters. A high-rated core with weak hardware or poorly designed seals will fail early.
- Incorrect Standard Application: Claiming a BS 476-22 FD60 rating is equivalent to an EN 1634-1 EI60 rating is misleading. The tests have significant differences. Specify the exact standard required by your jurisdiction/design.
- Ignoring Hardware Impact: Using non-certified or incorrectly installed hardware (wrong hinge type, fewer hinges, wrong closer) instantly downgrades the entire assembly’s rating to zero.
- Glazing Oversights: Exceeding the maximum certified glazed area or using non-certified glass/beads invalidates the rating. Suppliers must provide glazing charts for each door/rating combination.
- Assuming Higher is Always Better: While safety margins are prudent, overspecifying ratings (e.g., requiring EI120 where EI60 suffices) adds unnecessary cost and weight, potentially straining hinges and closers, and complicating installation. Specify precisely what the design requires.
The Buyer’s Action Plan: Specifying & Verifying Ratings with Precision
- Know Your Requirement: Work with your architect, fire engineer, and code consultant to determine the exact minimum required fire rating (including Integrity AND Insulation – EI or equivalent) for each specific door location based on the approved fire strategy and local regulations. Document this in your specification.
- Specify Explicitly & Completely: In your RFQ/RFP, state for each door type/location:
- Required Fire Resistance Rating (e.g., EI 60 per EN 1634-1, UL 90 min per UL 10C, FD60S per BS 476-22).
- The exact standard required.
- Any specific requirements for glazing (max size, type), hardware (e.g., specific closer grade), or seals (smoke seals required?).
- Mandate that the rating applies to the complete assembly as supplied.
- Demand Assembly-Specific Proof: Require bidders to submit, for each door type/rating combination quoted:
- Valid Classification Certificate / UL Listing.
- Full Fire Test Report (or clearly referenced extract) proving the EI/UL/FD rating.
- Tested Specification Sheet detailing the exact configuration that achieved the rating.
- Glazing charts (if applicable).
- Forensic Verification:
- Match the Rating: Does the certificate/report show the exact EI/UL/FD rating you specified?
- Match the Standard: Was it tested to the standard you specified (EN 1634-1, UL 10C, BS 476-22)?
- Match the Assembly: Does the Tested Spec Sheet match the door leaf, frame, and every single hardware component you are buying? Pay obsessive attention to hinge model/placement, lock model, closer model, seal type/location.
- Check Glazing: Does the proposed vision panel size/area fall within the limits stated on the glazing chart for that specific rating and door leaf?
- Verify Validity: Are the certificate and supporting FPC audits current?
- Label Verification: Ensure your contract mandates the physical presence of the correct certification label (showing the EI/UL/FD rating) on the door and frame. Verify this upon delivery.
4. What Core Materials and Steel Types Are Used in the Fire Doors?
The Hidden Anatomy of Safety: Why Core Materials & Steel Specifications Are Make-or-Break for Fire Door Integrity
In the quest for certified fire doors, focusing solely on the rating stamped on a label is like judging a car’s safety by its paint job. The true determinants of performance – the ability to withstand hellish temperatures, maintain structural integrity, and block lethal heat transfer – lie buried within: the core material and the steel substrate. Asking a supplier, “What core materials and steel types are used?” isn’t a technical nicety; it’s a fundamental interrogation of the door’s engineered DNA. Compromise here, and even a “certified” door becomes a catastrophic liability. Here’s why materials matter profoundly and how to dissect supplier claims.
Beyond the Skin: The Critical Role of Core Materials
The core is the heart of the fire door, responsible for the bulk of its insulating properties (I-rating) and contributing significantly to integrity (E-rating). Its performance under fire is governed by complex physics – endothermic reactions, char formation, gas evolution, and thermal stability. Not all cores are created equal, even if they claim the same nominal rating.
- Mineral Wool (Rockwool/Stonewool):
- The Gold Standard: Widely regarded as the premium core for high-performance steel fire doors (EI 60, 90, 120+ min). Composed of spun volcanic rock or slag, bonded with thermosetting resin.
- Performance Advantages:
- Exceptional Insulation: Non-combustible (A1/A2-s1,d0 Euroclass), with very low thermal conductivity. Excels at limiting temperature rise on the unexposed face.
- Stability: Maintains dimensional stability under intense, prolonged heat. Doesn’t slump, shrink excessively, or produce significant smoke/debris that could compromise seals or glazing beads.
- High Melting Point: Typically exceeds 1000°C.
- Sound Insulation: Offers excellent acoustic performance as a secondary benefit.
- Density is Critical: Performance is directly tied to core density (typically 110-170 kg/m³ for fire doors). Demand the exact density specification used in the certified assembly. Lower density = poorer performance. Suppliers using low-density mineral wool to cut costs are compromising safety.
- Bonding Matters: The core must be securely bonded to the steel facings using high-temperature intumescent adhesive throughout its entire surface area. Delamination under heat is a critical failure point. Ask about the bonding process and adhesive specification.
- Gypsum-Based Cores:
- Common & Cost-Effective: Often used for EI 30 and EI 60 timber or steel doors. Composed of gypsum plaster, often reinforced with additives (e.g., vermiculite, glass fibres).
- Performance:
- Good Initial Insulation: Relies on endothermic dehydration (release of chemically bound water vapor) to absorb heat.
- Potential Limitations: Can shrink and crack significantly during prolonged fire exposure, potentially compromising integrity and insulation over longer durations (e.g., EI 90/120). Structural stability after water release can be a concern. More susceptible to impact damage during handling/use.
- Specification Scrutiny: Density, reinforcement type/percentage, and exact formulation are crucial. Not all gypsum cores are equivalent. Demand details.
- Vermiculite/Perlite Cores:
- Less Common in High-Rating Steel Doors: Expanded minerals (vermiculite/perlite) bound with cementitious or silicate binders.
- Performance: Lightweight, non-combustible, but generally offers lower insulation performance than high-density mineral wool for the same thickness. More commonly found in older specs or lower ratings.
- Density & Binder Critical: Performance heavily depends on density and the quality/quantity of the binder.
- Composite Cores (e.g., Honeycomb with Intumescent Fill):
- Niche Applications: Sometimes used for lightweight doors requiring specific ratings. Involves a structural honeycomb (e.g., cardboard, mineral board) filled with intumescent granules or paste.
- Performance Risk: Requires extremely rigorous testing and quality control. Potential for inconsistent fill, core instability under heat, or reliance on the honeycomb material’s combustibility. Demand exhaustive proof of certification for the exact composite configuration.
- Intumescent Sheets/Layers: While not a “core” per se, these are critical components integrated with the core or applied to surfaces. They expand dramatically under heat (often 5-50x volume) to seal gaps around the door edge, within glazing beads, and around hardware penetrations. Ask: “What specific intumescent sealant products (manufacturer, model) are used in the certified door edge and glazing system? What temperature do they activate at?”
The Steel Skeleton: More Than Just “Metal”
The steel facings and frame provide structural integrity, impact resistance, and form the substrate for the core and intumescent seals. The devil is in the metallurgical details:
- Steel Grade & Quality:
- Cold-Rolled Mild Steel (CRCA): The standard for most fire door skins and frames. Demand the specific grade/thickness (gauge):
- Skin Thickness: Typically 0.6mm to 1.2mm. Thicker steel (e.g., 0.8mm, 1.0mm) offers better impact resistance, dent resistance, and contributes to overall rigidity during fire exposure. Beware suppliers using ultra-thin 0.5mm skins prone to warping and damage. The certified spec sheet must state the exact gauge.
- Frame Thickness: Frames often use thicker steel than skins (e.g., 1.2mm, 1.5mm) for rigidity and secure fixing. Check the spec.
- Coating: Primed (ZP – Zinc Phosphate) and painted (polyester powder coat is common) for corrosion resistance. Galvanized steel (GI) is also used, especially in corrosive environments. Specify corrosion protection requirements.
- Cold-Rolled Mild Steel (CRCA): The standard for most fire door skins and frames. Demand the specific grade/thickness (gauge):
- Fabrication Integrity:
- Seam Welding: How are the door edges and corners joined? Continuous laser welding or high-frequency (HF) welding provides superior strength, airtightness, and resistance to warping under heat compared to spot welding or mechanical folding alone. Ask about the welding method.
- Frame Construction: Are frames welded or mechanically fastened? Welded corners are stronger and more dimensionally stable. How is the door stop formed and attached?
- Stiffening: How is door leaf rigidity maintained? Internal steel stiffeners (channels, profiles) around the perimeter and behind hardware points are essential, especially for larger doors or those with glazing. Ask: “Are internal perimeter and hardware reinforcement channels included? What gauge steel are they made from?”
- The Frame-Door Interface: This is a critical failure point. The frame profile must be designed to accommodate the intumescent seals correctly and ensure proper alignment and compression when the door closes. Ask: “Show me the certified detail of the seal location within the frame profile for this specific assembly.”
Why Generic Answers Are Red Flags: Demanding Material Transparency
A supplier stating “mineral wool core” or “steel construction” is utterly inadequate. Here’s what you MUST uncover:
- Core Material SPECIFICS:
- “What is the EXACT core material type (e.g., high-density stone wool, specific gypsum formulation)?”
- “What is the CERTIFIED density (in kg/m³) used in the assembly achieving the EI XX / UL XX min rating?”
- “Who is the core material manufacturer? Provide the material data sheet (MDS) and fire performance certificate (e.g., Euroclass A1 reaction to fire).”
- “What high-temperature adhesive bonds the core to the skins? Provide the product name and technical data.”
- “For glazed doors: What is the certified core material and method used around the vision panel aperture?”
- Steel SPECIFICS:
- “What is the EXACT thickness (gauge in mm) of the door facings specified in the certified assembly?”
- “What is the EXACT thickness (gauge in mm) and profile design of the door frame?”
- “What steel grade/coating is used (e.g., CRCA ZP 0.8mm)?”
- “Are internal perimeter and hardware reinforcement channels used? What gauge steel? Show the detail on the certified spec sheet.”
- “What welding method is used for door edge seams and frame corners (e.g., continuous laser, HF)?”
- The Certification Link – THE MOST CRITICAL POINT:
- “Show me the Fire Test Report and Tested Specification Sheet that explicitly lists the core material type, density, manufacturer, adhesive type, steel gauges for skins/frame/stiffeners, and welding methods used in the exactly tested assembly achieving the claimed EI/UL rating.” ANY deviation from these material specs invalidates the certification.
The Material Compromise Trap: How Suppliers Cut Corners (and Safety)
- “Density Downgrading”: Using lower-density mineral wool than certified to save cost. This directly reduces insulation performance.
- “Core Swapping”: Substituting a cheaper, uncertified gypsum or vermiculite core for mineral wool after certification was achieved with mineral wool.
- “Skinny Steel”: Using thinner-gauge steel skins or frame profiles than certified, compromising rigidity and warping resistance under fire.
- “Invisible Inferiority”: Using non-certified or lower-specification adhesives, leading to core delamination.
- “Missing Muscle”: Omitting internal stiffeners or using lighter-gauge stiffeners, allowing the door to distort and fail prematurely.
- “Seal Shortcuts”: Using cheaper, slower-activating, or less expansive intumescent seals than those specified in the test report.
The Buyer’s Forensic Material Audit
- Enshrine Specifics in Specification: Your RFQ/RFP must mandate:
- Core material type, manufacturer, density (kg/m³), and bonding adhesive specification.
- Skin steel gauge, grade, and coating.
- Frame steel gauge, profile type, and coating.
- Internal reinforcement details (gauge, location).
- Welding methods.
- Explicit requirement that these materials MUST match the certified tested specification sheet exactly.
- Demand Certified Documentation: Require submission of:
- The Tested Specification Sheet listing all material specs.
- The Full Fire Test Report confirming the materials used in the test.
- Material Data Sheets (MDS) and fire reaction certificates (e.g., Euroclass) for the core.
- Adhesive technical data sheet.
- Scrutinize the Tested Spec Sheet: Line-by-line verification:
- Does the core material and density match?
- Do the skin and frame gauges match?
- Are the stiffeners detailed? Gauge?
- Is the welding method stated?
- Are the intumescent seal products specified?
- Verify During Production (If Possible): For large projects, consider factory audits or third-party inspection to verify material compliance against the certified spec and your PO before shipment. Check material delivery notes and mill certificates for steel.
- Sample Verification: Upon receiving pre-production or initial samples, physically measure steel thickness (using a micrometer) at multiple points. Compare core material visually/density (if accessible via hardware cutouts, though this is destructive) against certified specs. Check for presence of internal stiffeners (magnet test or weight/rigidity check).
5. Do You Manufacture the Entire Door Assembly, Including Frame and Hardware?
The System Integrity Imperative: Why “Full Assembly” Manufacturing is Non-Negotiable for Certified Fire Doors
Asking a supplier, “Do you manufacture the entire door assembly, including the frame and hardware?” cuts to the heart of fire door integrity. This isn’t about vertical integration for efficiency—it’s a life-safety imperative. Compartmentation hinges on the tested interaction of every component under fire conditions. When frames, hardware, or seals are outsourced, mismatched, or installed inconsistently, certification evaporates—and so does your protection.
Why Full Assembly Control Matters: The Certification Time Bomb
Fire door certifications (UL, EN, BS) apply only to the exact assembly tested—a precise recipe of door leaf, frame, hinges, latches, seals, and installation methods. Deviate by a single hinge model, seal location, or frame anchor, and the rating is nullified.
Critical Risks of Multi-Source Suppliers:
- Certification Decoupling
- A supplier manufacturing only the door leaf relies on third-party frames/hardware.
- Result: The certified test report is void. The “system” was never tested together.
- Example: A door leaf tested with Frame A and Hinge B won’t perform the same with Frame C or Hinge D.
- Accountability Black Holes
- When defects arise, finger-pointing begins: “The hinge failed? Not our fault—talk to the hardware supplier.”
- No single entity owns full system liability.
- Inconsistent Quality Gates
- Outsourced components lack integrated quality control. A frame manufacturer’s tolerance variance can misalign hinges, compromising seal activation.
- Installation Chaos
- Contractors juggling components from 3+ suppliers amplify error risks (e.g., wrong seals, misplaced hinges).
The “Full Assembly” Litmus Test: What Suppliers MUST Prove
✅ 1. Vertical Manufacturing Scope
- Demand Evidence:
- Factory audits showing in-house production of:
- Door leaves (skin cutting, core bonding, pressing, welding)
- Frames (steel profiling, corner welding, seal groove machining)
- Hardware integration (hinge prep, lock prep, seal application)
- Factory audits showing in-house production of:
- Red Flag: “We partner with certified frame/hardware suppliers.” Partnerships ≠ control.
✅ 2. Single-Source Certification
- Certificates must list the supplier as system certifier—not just door leaf certifier.
- Key Documents:
- Test reports showing the supplier’s own frame and hardware in the furnace.
- Scope statements covering the complete assembly (e.g., “Door Leaf Model X + Frame Profile Y + Hinge Z”).
- Example: UL listings include “Frame Manufacturer” and “Hardware Configurations.”
✅ 3. Hardware Sovereignty
- Critical Question:“Do you manufacture or specification-lock ALL hardware?”
- Hinges: Must be identical to tested model (material, ball bearings, pin diameter).
- Seals: Intumescent brand, expansion ratio, groove dimensions.
- Closers: Adjustable vs. non-adjustable, force rating.
- Acceptable Model: Supplier-owned designs made by sub-contractors under tight specification—with test validation.
✅ 4. Integrated Quality Control
- Assembly-line checks for:
- Frame/door alignment before hinge fitting
- Seal groove depth/cleanliness
- Hardware torque tolerances
- Demand: Evidence of dimensional audits at each assembly stage.
The Cost of Fragmentation: Real-World Failures
🔥 Case 1: The Outsourced Frame Disaster
- Scenario: A “certified” EI 60 door leaf installed with a frame from a cheaper supplier.
- Failure: Frame profile lacked the tested intumescent seal groove depth.
- Result: Seals didn’t compress. Flames breached in 28 minutes.
🔥 Case 2: Hardware “Equivalency” Trap
- Scenario: Supplier substituted tested hinges with “similar” off-the-shelf models.
- Failure: Inferior bearings deformed under heat, causing door sag and gap formation.
- Result: Integrity failure at 42 minutes (EI 60 required).
The Buyer’s Action Plan: Verifying True Assembly Control
1. Pre-Qualification Interrogation
- “Show me your factory production process for frames and hardware integration.”
- “Provide a video tour of your frame fabrication and assembly line.”
2. Certification Autopsy
- Cross-check test reports:
- Is the frame manufacturer the same as the door supplier?
- Are hardware part numbers listed? Do they match current offerings?
- Does the scope cover all variables (e.g., anchor spacing)?
3. Supply Chain Transparency
- Demand: A full disclosure of outsourced components.
- Verify: Sub-supplier certifications (e.g., hinge ISO 9001, seal fire reports).
4. Witness Testing (For Critical Projects)
- Require observation of assembly integration during factory audits.
- Check: Seal application, hinge mounting, frame welding.
5. Contractual Armor
- Mandate:
- “Supplier warrants full responsibility for the certified assembly, including all components.”
- “Substitution of any part voids certification and triggers liquidated damages.”
Global Variations: Regulatory Teeth
- EU/UK: EN 16034 mandates “complete door set” (leaf + frame + hardware) certification.
- USA: NFPA 80 requires listed assemblies—installers can’t mix-and-match components.
- Australia: AS 1905.1 demands evidence of compatible components.
The Lifeline After the Sale: Why Lead Time Realism & After-Sales Strength Define a Trustworthy Fire Door Manufacturer
At YK Fire Door Manufacturer, we believe that securing certified fire rated doors is only the beginning. What truly defines a dependable supplier is not just the door’s fire rating—it’s the operational transparency and long-term commitment behind that product. Two often-overlooked pillars—realistic lead times and robust after-sales support—form the safety net that ultimately protects lives, property, and your project’s compliance.
When you ask a fire door supplier: “What is your lead time and after-sales service policy?”—you’re not just ticking off a logistics checklist. You’re stress-testing their operational integrity, their quality control maturity, and their ability to uphold safety over decades. Any failure in these areas turns even the best-rated wooden fire resistant doors or steel commercial doors into latent liabilities.
The Lead Time Mirage: When “8 Weeks” Becomes a Dangerous Illusion
In the fire door industry, unrealistic promises are all too common. Many commercial door manufacturers quote standard 6–8 week lead times for all products, but industry veterans know this is a red flag. Lead time reflects not just production efficiency but the integrity of testing, sourcing, and assembly.
At YK, we produce everything from 90 minute fire rated wood doors to customized fire door garage assemblies and fire exit doors. These products require detailed scheduling due to:
Certification-Driven Production:
- Component Traceability: We batch-test all core materials—whether it’s mineral wool for fire rated wood doors or stainless steel components for fire rated steel doors.
- In-Process QA: Every stage involves density verification, weld integrity checks, and dimensional control. Quality slows down production—for good reason.
- Third-Party Inspection (TPI): Particularly in healthcare or high-rise projects, independent inspectors review core bonding, seal placement, and fire-resistant glazing. That inspection time is essential—not optional.
Material Science Realities:
- Core Stabilization: Whether it’s wooden fire doors or gypsum-core doorsets, curing time can’t be rushed. Any shortcut risks catastrophic failure under heat.
- Coating Integrity: Powder coating for our steel commercial doors involves precise heat cycles to ensure corrosion resistance and fire integrity.
Customization Complexities:
- Fire-Rated Glazing: Our fire rated glass panels—gel-filled or ceramic—require additional sourcing and certification.
- Electromagnetic Hardware Integration: We engineer fully integrated fire rated door systems with magnetic locks and advanced access control. These are not plug-and-play installations.
- Frame Profiles: Non-standard applications such as curved wall fire doors or blast-resistant frames demand custom fabrication.
Global Supply Chain Vulnerabilities:
Unlike many suppliers, YK Fire Door is vertically integrated across our sourcing operations in China, enabling us to avoid most single points of failure. We don’t substitute uncertified hinges or seals. Doing so would invalidate your fire rating, especially under EN 1634 or UL 10C standards.
Lead Time Red Flags to Watch For:
- “All doors in 6–8 weeks” — A general promise that ignores customization complexity.
- No review of hardware or project specifics — Indicative of poor planning.
- Offers to “expedite” without QA detail — Suggests shortcuts will be taken.
- No production schedule available — Indicates lack of manufacturing discipline.
6.What Is Your Lead Time and After-Sales Support Policy?
After-Sales Support: Where YK’s Commitment Extends Beyond Installation
As a trusted fire rated door company, YK doesn’t see fire doors as static installations. They are dynamic, regulatory devices—subject to use, abuse, environmental factors, and evolving safety standards. Our after-sales service is designed to maintain fire certification compliance for 20+ years across global jurisdictions, including stringent fire door regulations in the UK, EU, Middle East, and Southeast Asia.
Our After-Sales Ecosystem Includes:
1. Long-Term Warranties That Matter
- Beyond the superficial paint or finish warranties, we offer performance-based coverage on:
- Core delamination
- Seal failure (intumescent or cold smoke)
- Premature hardware wear (hinges, closers)
- Corrosion-related structural issues
- These warranties are enforceable for up to 10 years—and void only when unapproved modifications are made.
2. Digital Door Dossiers
Every door installed—be it a fire rated wood door in a school or a steel fire door in a logistics warehouse—comes with a digital, project-specific dossier:
- Certified “as-built” specs
- Detailed installation documentation (anchor types, seal positions, hinge models)
- Maintenance templates tied to door ID labels
- Cloud access for clients, inspectors, and facility teams
This digital trail is updated automatically when approved retrofits occur.
3. Global Technical Support
Unlike some suppliers, YK doesn’t outsource support to sales teams. We maintain a network of fire door engineers trained in forensics, failure diagnostics, and field compliance.
- Root-cause analysis for seal failures or latch issues
- Certified repair kits for field use (no generic hardware allowed)
- 72-hour global escalation response for technical faults
4. OEM Spare Parts Policy
We commit to stocking exact certified components—whether for door closer fire regulations or smoke seals—for 15+ years. If you need a specific hinge or closer 10 years from now, we’ll have it.
5. Retrofit Engineering with Certification Compliance
We support clients in requesting safe modifications—vision panel inserts, lock changes, or automation—while coordinating with test labs for possible re-certification. All with transparent re-testing and documentation fees.
YK Door Industry-A model template for fire door manufacturers
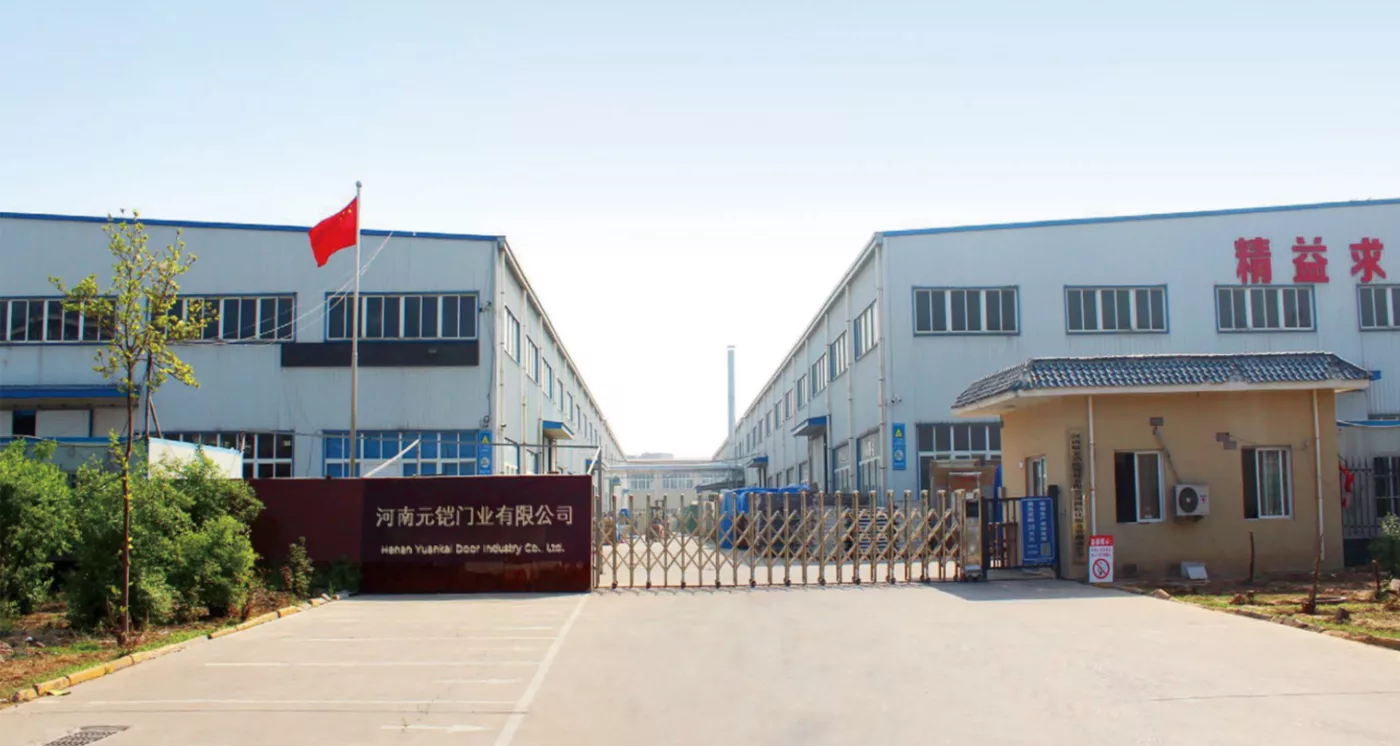
A certified fire door is far more than a panel of wood or steel—it’s a critical life-safety system that must withstand heat, pressure, smoke, and time. Its performance during emergencies directly determines how much time people have to evacuate, how effectively fire is contained, and whether a building remains code-compliant in the eyes of regulators and insurers. That’s why choosing the right fire door manufacturer is not simply a procurement task—it’s a strategic safety decision.
By asking these six essential questions, you can separate generic vendors from professional fire door suppliers who understand international fire door regulations, building regulations for fire doors, and the engineering that goes into long-lasting protection. At YK Fire Door, we’ve built our reputation as a trusted China fire door manufacturer by combining certified production, technical precision, and end-to-end service.
From 90 minute fire rated wood doors for schools and hospitals to fire door garage assemblies, fire exit doors, and heavy-duty steel commercial door systems, we help our clients meet both code and conscience. A high-quality fire rated door company delivers more than just products—it delivers long-term compliance, documented safety, and total confidence. Before you finalize your next fire door purchase, make sure your manufacturer can prove they’re not just compliant today—but prepared for the demands of tomorrow.
# | Question | YK’s Answer |
---|---|---|
1 | Are your fire doors certified (e.g., UL, CE, EN)? | Yes, our fire doors are certified to UL 10C, EN 1634, and CE standards. |
2 | Can you provide valid fire test reports and classification certificates? | Yes, all test reports and classification certificates are available and up to date. |
3 | What fire ratings are available? | 30min, 60min, 90min, and 120min ratings are available. |
4 | What materials do you use in the doors? | Galvanized steel with honeycomb, rock wool, or vermiculite core. |
5 | Do you produce the entire door assembly? | Yes, we manufacture door leaf, frame, and certified fire-rated hardware. |
6 | Is your factory ISO certified or audited? | Yes, our factory is ISO 9001 certified and undergoes regular third-party audits. |
7 | Can you customize size, finish, and glazing? | Yes, we offer full customization including color, size, and fire-rated glass options. |
8 | How do you ensure quality consistency? | Through strict QC processes, full inspection per batch, and traceable records. |
9 | Do you have experience with export projects? | Yes, we export to over 30 countries and are familiar with local compliance requirements. |
10 | What is your lead time and after-sales policy? | Standard lead time is 20–30 days. We offer technical support, warranties, and spare parts. |